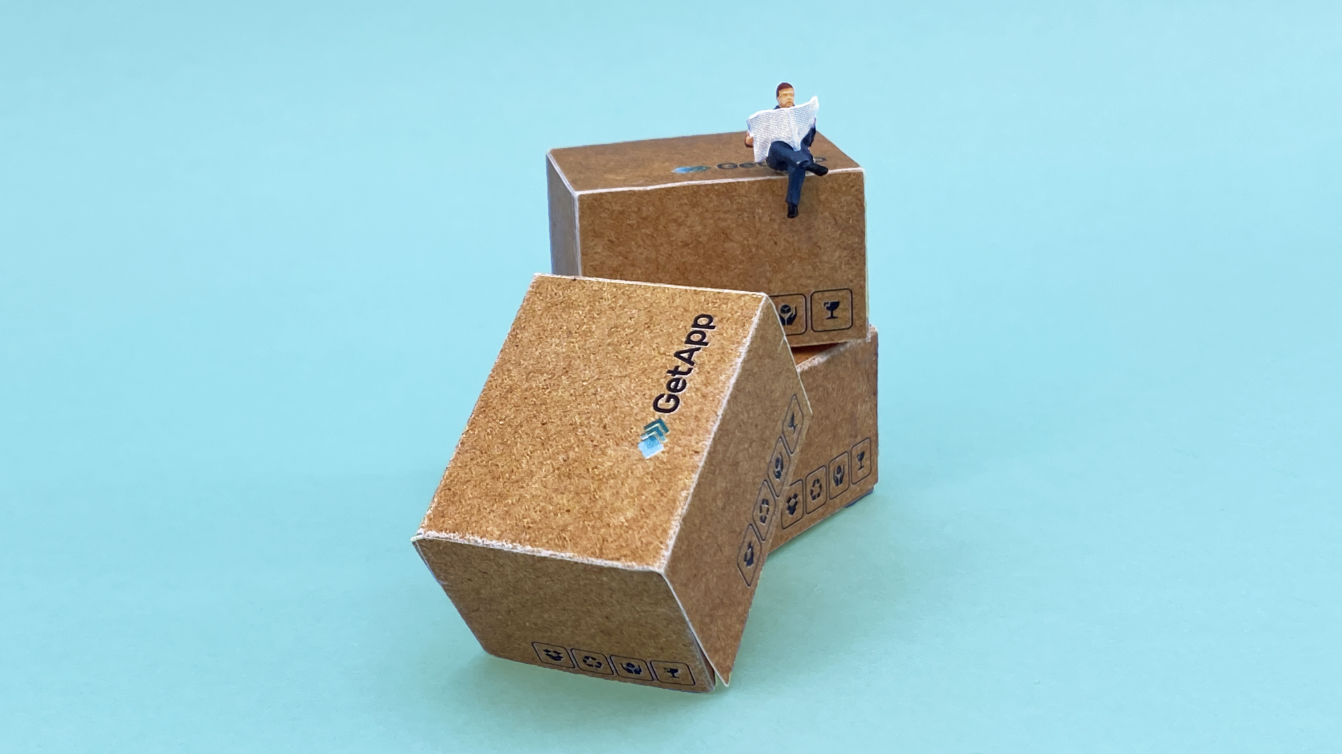
Lead Time in Inventory Management: A Scientific System to Measure Work Tendency
In any business, inventory management plays a crucial role in ensuring the smooth flow of operations. Sufficient stocks of products must be available to meet customer demand, while also minimizing holding costs and maximizing profitability. However, achieving this balance is not always easy, especially when dealing with a complex supply chain with multiple suppliers and distributors. One concept that can help in these situations is Lead Time. This article will discuss what Lead Time is and how it can be used in inventory management.
What is Lead Time?
Lead Time refers to the time between placing an order and receiving the goods or services required for production, sales or any other business activity. It is the total time required for the supplier to process an order, manufacture the goods, package them, ship them, and deliver them to the buyer. It is a critical aspect of inventory management because it ensures that the company has an appropriate level of inventory to meet customer demand without incurring unnecessary costs.
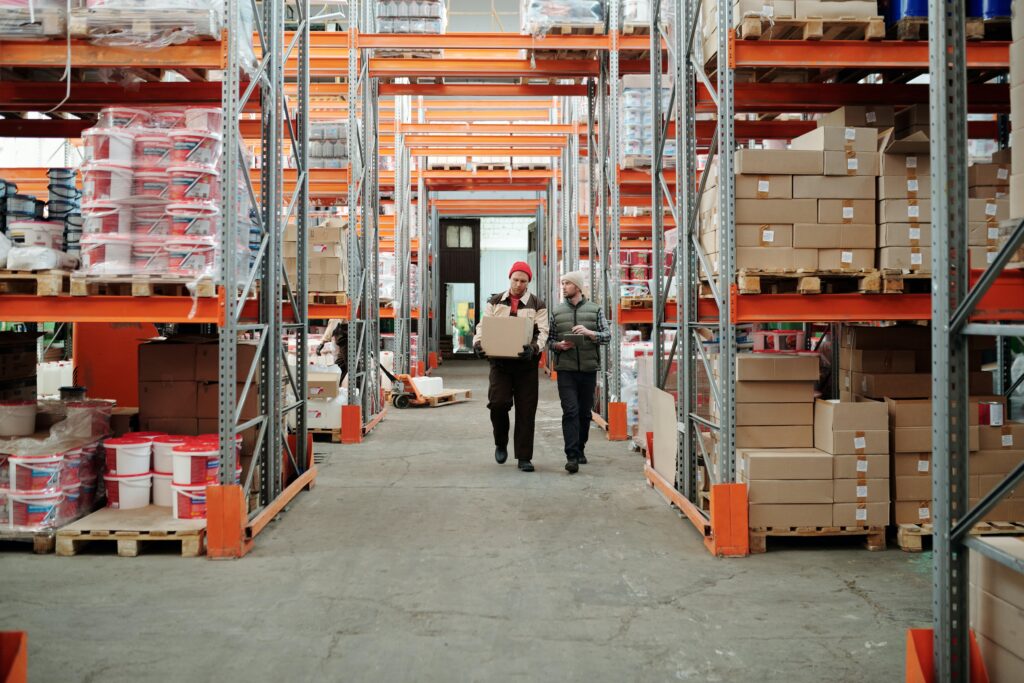
Why is Lead Time important in inventory management?
Lead Time plays a crucial role in inventory management because it helps businesses to calculate the amount of inventory they need to keep on hand at any given time. By understanding Lead Time, a business can forecast its inventory requirements more accurately, enabling it to reduce inventory levels and lower carrying costs, while still responding quickly to customer demand. Lead Time is also essential when deciding when to place orders to avoid stockouts and ensure that the business can fulfill customer orders on time.
Moreover, Lead Time can help businesses to measure the effectiveness of their internal processes and identify areas for improvement. By analyzing Lead Time data, businesses can identify bottlenecks in their supply chain, improve communication with suppliers, and streamline their operations. This can lead to improved lead times, reduced costs, and increased efficiency, benefiting both the company and its customers.
How to calculate Lead Time?
To calculate Lead Time, businesses need to consider several factors, including:
1. Order Processing Time: The time it takes for the supplier to process the order, which includes checking inventory availability, creating a purchase order, and issuing an invoice.
2. Manufacturing Time: The time it takes to manufacture the goods, including any delays due to production or quality issues.
3. Packaging Time: The time it takes to pack the goods, including any custom packaging requirements.
4. Shipping Time: The time it takes to ship the goods from the supplier to the buyer, including any delays due to carrier delays or customs clearance.
5. Delivery Time: The time it takes for the goods to reach the customer after they have been shipped.
Once these factors have been considered, businesses can calculate Lead Time by adding up the processing time, manufacturing time, packaging time, shipping time and delivery time for each order.
How can businesses improve Lead Time?
Businesses can improve Lead Time by adopting strategies such as:
1. Reducing Order Processing Time: By automating the procurement process and improving communication with suppliers, businesses can reduce order processing time, which can result in faster Lead Times.
2. Streamlining Production: By optimizing production processes, businesses can reduce manufacturing time, which can lead to shorter Lead Times.
3. Improving Packaging and Shipping: By improving packaging and shipping processes, businesses can reduce the time it takes to pack and ship goods, which can shorten Lead Times.
4. Storing Inventory Closer to Customers: By strategically placing inventory closer to customers, businesses can reduce delivery times, which can improve Lead Times.
Conclusion
In summary, Lead Time is a critical concept in inventory management that helps businesses to understand the time required to receive goods or services required for production, sales or any other business activity. By accurately calculating Lead Time and improving processes, businesses can reduce inventory levels, reduce costs, and ensure timely deliveries, thereby increasing efficiency, and customer satisfaction. Jiangsu Caisheng New Energy Technology Co., Ltd. has established itself as a prominent player in the solar energy industry, providing a range of high-quality products to customers worldwide, including solar panels, solar street lamps, energy storage batteries, inverters, wires and cables, meter boxes, photovoltaic support and other import and export business. Their emphasis on quality, innovation, and reliability has helped them to build a reputation as a trusted supplier of solar energy products.